Material Finishes
Material Finishes and Quality Standards
Dio-Met Fabrications Ltd are committed to supplying high quality products that are made to last and as such, we have introduced quality provisions in accordance with our in-house quality procedures under the externally audited remit of BS EN1090-2 and ISO 9001. The following material finishes are therefore deemed acceptable, and of expected quality:
Galvanized Steel (hot dip galvanizing)
Galvanizing is an industrial finish which involves immersing steel into molten zinc to obtain a coating. The bonded coating is formed to protect steel in harsh environments, whether they be internal or external. When welding sections of steel together, even if ‘flushed’ off, the weld will always show through in the galvanizing, as per the below example :

Any hollow steel product must be vented before galvanizing to allow air to be evacuated from within and around the fabrication allowing it to be completely immersed. The vent holes also prevent the build up of pressure which can rupture the steel. Vent holes are usually required to be placed on external corners and tube ends and where viable done as discreetly as possible, typical images below :

When removed from the galvanizing bath, the zinc solution will often form drips and gather in pools on certain areas of the steel product; this can produce a rough surface or concentrated hard lumps of zinc solution. For galvanized only products, the material is fettled with files to remove as much of the build up as possible, whilst maintaining the coating. Over-fettling could potentially go beneath the zinc coating to expose the raw steel and cause rusting over time. Example below of zinc build up, prior to fettling :
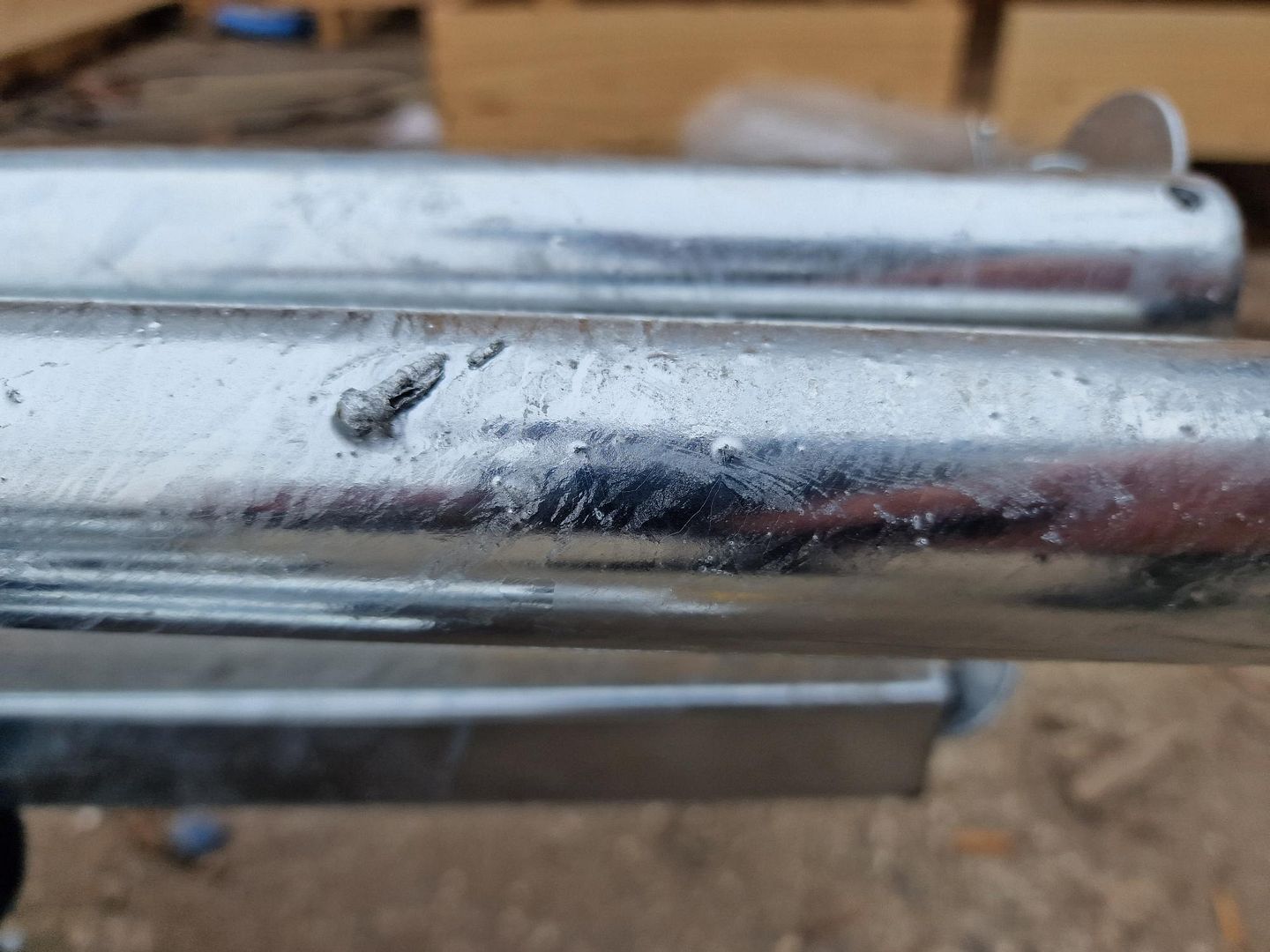
Powercoated Steel
Powdercoating is the application of a smooth paint finish to steelwork. When powdercoating onto raw steel, some scale or texture may be visible at close range. A typical powdercoated (only) finish can be seen below :
When used externally, all mild steel should first be galvanized (see notes above), fettled, t-washed and then powdercoated. If material is not both galvanized and t-washed with a mordant solution, the powdercoating would have the tendancy to flake from the steel- it is also not suitable to use a powdercoated only product externally. Refer to the description above on galvanizing and the formation of zinc build up, it is therefore expected that some minor rough patches will be seen through the powdercoating, even after careful fettling :
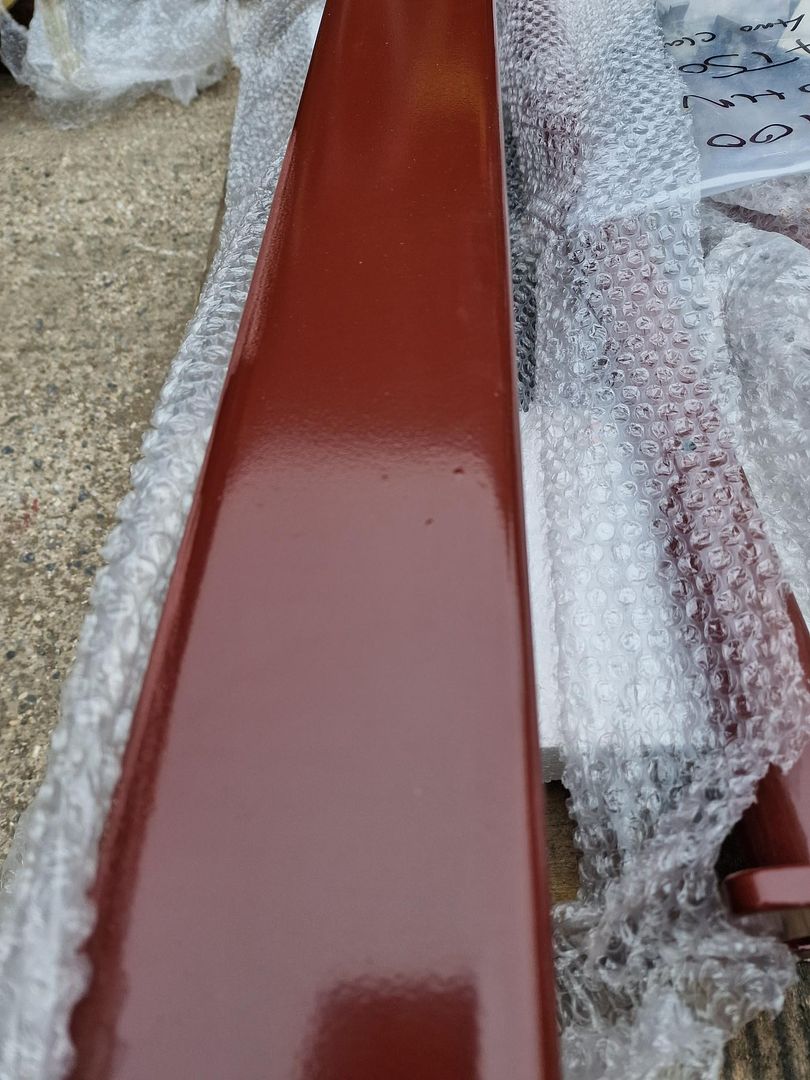
Given the notes on galvanizing, above, it is to be expected that some areas on a galvanized and powdercoated product would not appear as perfectly smooth as if the product had not first been galvanized. It is also unavoidable that any welded areas will also form a raised finish due to the galvanizing process, images below :
AWAITING IMAGE
The recognized industry standard for repairing powder-coated steel is to use a colour-matched aerosol spray. While the exact procedure and surface preparation may vary depending on the specific product, the general approach involves applying several light coats to gradually build up the paint finish to the desired level of coverage and protection. Given the realities of transporting, offloading, and installing substantial structures like staircases or balconies, it is reasonable to anticipate that despite the highest level of care, minor marks or scratches may occur. Consequently, minor touch-ups are considered a standard part of the installation process and are performed upon completion to ensure the product meets our stringent quality standards.
Stainless-Steel
Stainless steel depends on its passive layer for its corrosion resistance. This is a very thin chromium oxide layer formed on its surface when chromium is present at 10.5% or above. The underlying metal is not corrosion resistant. The passive layer forms spontaneously on a clean surface but can be damaged by iron contamination, airborne particles and particularly chlorides.
Therefore, it is imperative that stainless steel is subject to an ongoing maintenance and cleaning program. Remember it is stainLESS, not stainFREE.
Dio-Met recommend a routine cleaning programme for stainless steel every month however some harsh environments would require more regular cleaning such as coastal / high salt areas. All stainless steel we provide for internal use is 304G and all material for external use is 316G.
All welds will be polished and brushed finish (satin) unless otherwise agreed, to a minimum of 320grit for a high quality visual finish.
All stainless steel we use for external applications is 316 marine grade however if it has been installed a number of months amd tea-staining become visible its likely a maintenance issue as stainless cannot be simply left alone forever, it needs cleaning regularly to keep at its best like anything. ‘Tea staining’ if caught early enough, should be surface deep only and easily removed with any stainless steel cleaner.
See below example of Tea Staining
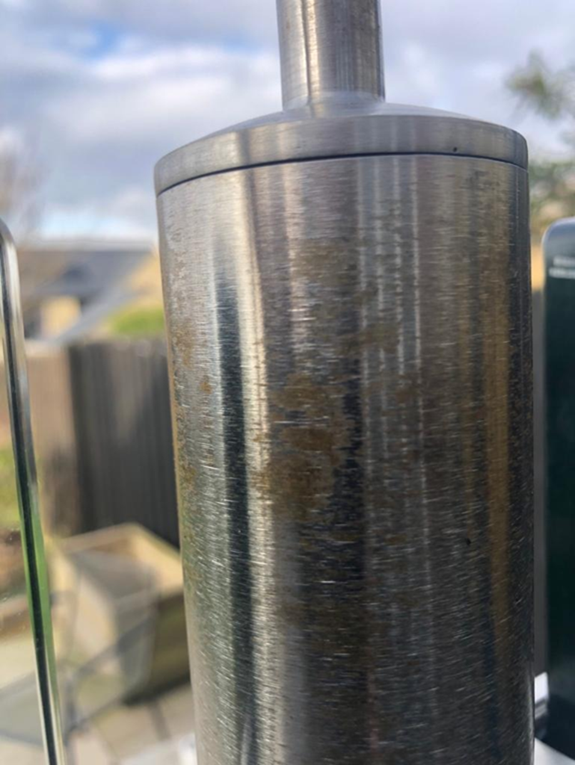
In coastal applications we would typically advise opting for a mirror polished stainless steel, since this does not have a ‘grain’ and thus makes it easier to clean and has less chance of salt or airbourne particles being retained on the steel and ultimately deteriorating the finish. Mirror polished stainless steel still requires maintainence, particulalry if used coastally, but such is significantly reduced when compared to a brushed (satin) polished finish. Mirror polished stainless steel as you might expect, is a more expensive option.
Toughened Glass
The Glass and Glazing Federation (GGF) have defined a glazing acceptability standard known as the GGF Visual quality standard for installed glass units constructed from flat transparent glass. This standard identifies all common visual issues found in glazing units and clarifies how imperfections should be assessed and what the acceptability for that standard is.
At Dio-Met we are selling a premium product and have thus identified that this acceptability standard does not meet the requirements of our customers. Therefore, we have produced a more stringent standard for us to adhere to giving our customers confidence that they will receive a glazing system that meets the same standard as the rest of our product. This acceptability standard is an additional guarantee on top of the GGF standard providing you with the utmost confidence that the products you receive will be of the highest quality.
1. Transparent glass used in the manufacture of insulating glass units is identical to that used traditionally for single sheet glass and will, therefore, have a similar level of quality.
2. Glazing shall be viewed at right angles to the glass from the room side at a distance of 1.5 metres in natural daylight and not in direct sunlight (a light box may be used for inspection as an alternative to natural daylight). The primary area to be viewed is the normal vision area, with the exception of a 25mm wide band around the perimeter of the unit. The secondary area to be viewed is the 25mm edge band.
3. Flat transparent glass, including laminated or toughened (tempered) glass shall be deemed acceptable if the following phenomena are neither obtrusive nor bunched: Seeds no larger than 1mm (1.5mm in the secondary area); bubbles or blisters; hairlines or blobs; fine scratches not more than 20mm long; minute embedded particles; Edge damage which does not affect the structural integrity of the glass. The presence of the following phenomena shall be deemed unacceptable: Scratches within the cavity; Dust/ debris from the spacer bar or integral bar cutting process should not be visible within the cavity; Scuffing or scratching to lead work; other extraneous materials within the cavity (eg hair, sealant etc), seeds larger than 1mm (1.5mm in the secondary area) Obtrusiveness of blemishes shall be judged by looking through the glass, not at it, under lighting conditions as described in section 2.
4. When thermally toughened (tempered) glass is viewed by reflection, the effect of the toughening process may be seen under certain lighting conditions. The visibility of surface coloration or patterns (Anisotropy) does not indicate deterioration in the physical performance of the toughened glass and the presence of this phenomenon will not be cause for rejection. Because of the nature of the toughening process, distortion can be introduced. Such distortion will be accentuated when the glass is viewed in reflection or incorporated in insulating glass units. The distortion will be deemed unacceptable if Newton’s Rings are visible. Other phenomena shall be assessed as per 3. Toughened glass is prone to bow and this should not exceed 2mm per linear m or localised bow should not exceed 0.5mm per 300mm.
5. Visible double reflection can occur under certain lighting aspect conditions, especially when viewed from an angle. This is an optical phenomenon arising from multiple surface reflections in laminated units.
6. The manufacture of flat laminated glass does not usually affect the visual quality of the glass incorporated in insulating glass units. However, the faults generally accepted in paragraph 3 may be increased in number by the fact that several layers of glass are used in the production of laminated glass. When viewed under certain light conditions, insulating glass units incorporating clear or tinted flat laminated glass may show a distortion effect caused by reflection on the multiple surfaces of the component of the laminated glass.
7. Safety glass will be manufactured with a visible stamp to comply with BS EN 6262-4:2005 and Part N of the Building Regulations. NOTE: The above criteria do not apply to Patterned Glass as, due to the method of manufacture, imperfections such as seeds and bubbles are deemed to be perfectly acceptable. Where sandblasted glass is supplied the blasted face will normally be positioned to the inside of the unit. When viewed from1.5m the sandblasted finish should appear consistent and free from hand/finger marks.
8. We produce toughened glass to a tolerance of +/- 2mm per metre- this tolerance is also applicable to laminated edges.
Natural Wood
The appearance of cracking and checking in natural wooden prodcuts such as our handrails or stair treads can be alarming at first, but rest assured that it's a natural part of timber's lifecycle. This is true not only for these prodcuts but for buildings, utensils, instruments, and ships. If you're concerned you've received a defective product and that the cracks you see are a sign of damage, we can attest that this is not a sign of deterioration but a natural reaction to climate.
Why Does Wood Split and Crack?
· Cracking and checking occur when the grain of timber reacts to the moisture level in the air.
· Wood adapts itself to the environment's moisture, temperature, and exposure to sunlight.
· This is known as equilibrium, where natural wood will shift with the climate around it.
This can be startling to those who have never owned organic or reclaimed wood products before, as they fear the item is of lesser quality, but it's simply nature's way of making itself at home. We have a particular affinity for natural wood products.
Should I Be Worried About Structural Integrity?
Not at all, unless the functionality of your stair or handrail is affected by cracks, there are no issues associated with the natural cracking of wood. If anything, checks and cracks are actually helpful in reinforcing structural integrity as it helps to release the tensions and pressure of shrinking or expanding wood. You can witness these changes throughout the seasons, as if your wood is a living, breathing being.
Can I Prevent Timber Cracking?
Because this is a natural process and wood is a natural product, it cannot be stopped only slowed. Our timber products and finishes used are chemical free, organic and help to keep the woods natural integrity, embracing its virgin qualities. Therefore, cracking may occur throughout its lifespan, particularly with any reclaimed wood.
However, if you are looking for ways to decelerate this process, we can recommend keeping your household at around 50% humidity by using a humidifier or dehumidifier. You can also avoid rooms that are excessively hot, dry, damp or that have direct sunlight throughout the day. These conditions help to prevent the possibility of natural wood cracking.
We cannot recommend any wax, polishes, or finishes at this time as we have never specifically tested such chemicals on our products. We do urge you to enjoy the organic beauty of your wood furniture, however, if you choose to use such preventative methods, try solutions sparingly at first to ensure it has the desired effect you are looking for.
Can I or Should I Repair Cracks in Timber?
In certain circumstances it may be an option to repair any cracks for aesthetic purposes (although we prefer the natural look of wood including any natural cracking, not everyone does!). Any suitable wood filler can be used and light sanding can be undertaken, re-oiling where required to restore the finish.
See below typical acceptable tread crack :
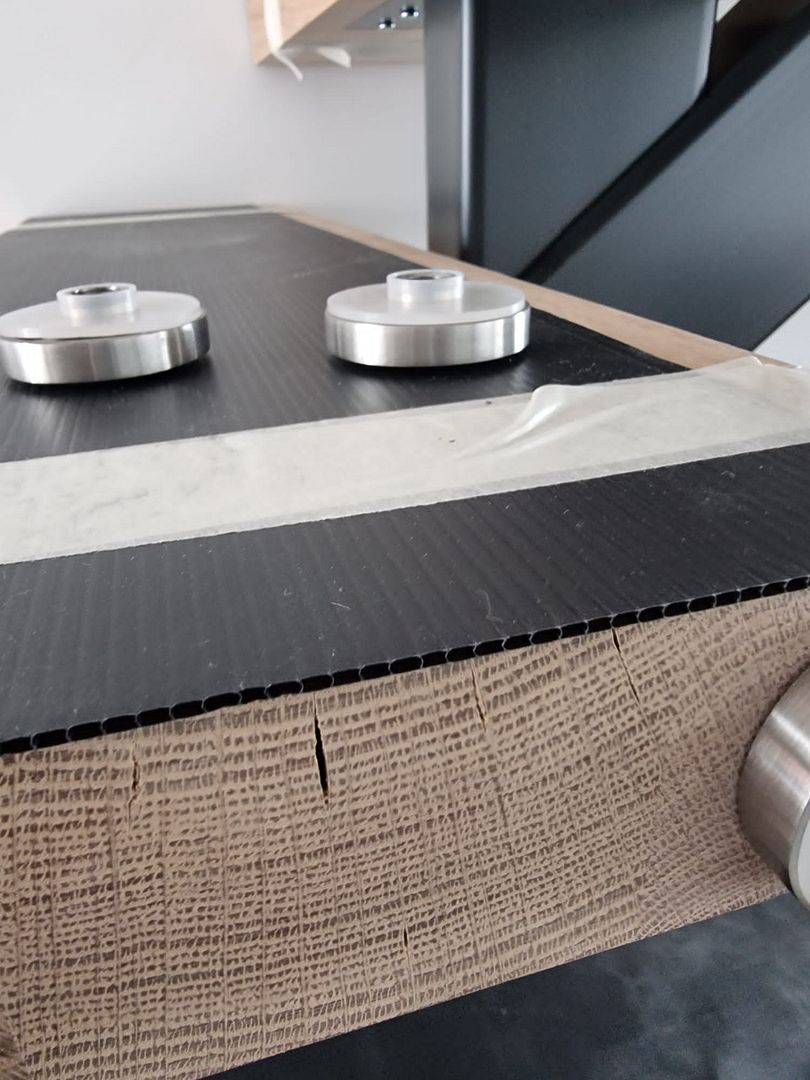